f you work in the construction industry, you are well aware of how technology is making fast-paced changes to this traditional sector. This blog addresses the challenges the industry faces and how technology is improving the bottom line as demonstrated in a use case with VIA IMC.
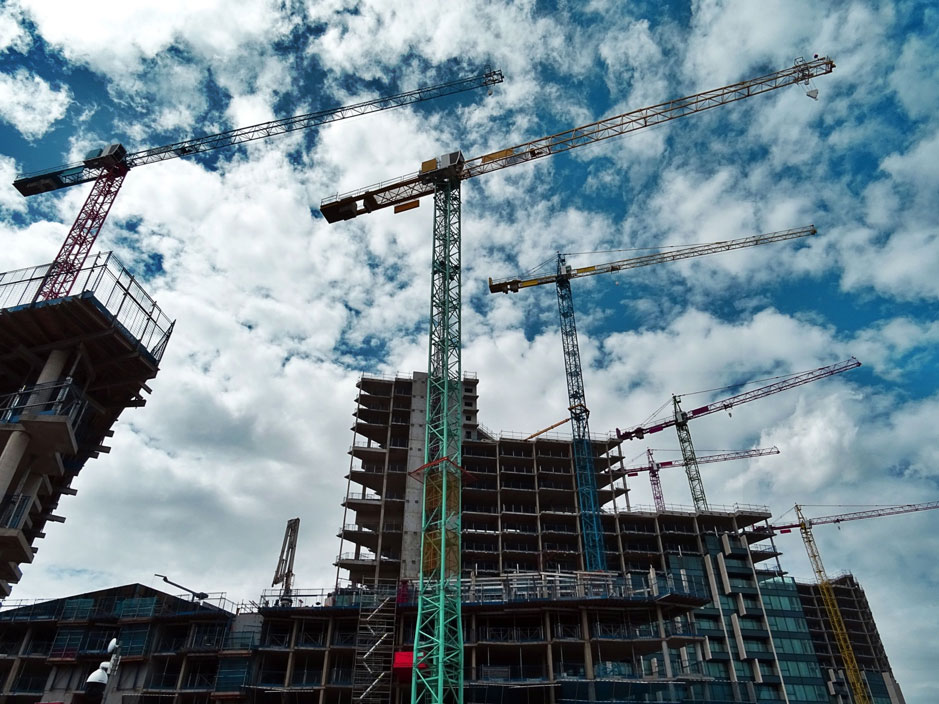
Fortune magazine describes the construction industry as “in love with drones.” Why? Intelligence gathered by drones allows construction companies to more efficiently deploy resources around a job site, trim costs and limit delays. Drones are being used in a variety of ways including inspections and the movement of materials and surveillance. Drones, using infrared capability, have even replaced the need to keep construction sites lit up at night for security purposes.
However, regardless of recent advances, the construction industry can still appear to be languishing in old habits and ways of thinking. If you would compare the construction industry with the manufacturing industry, you would conclude that improvement in productivity in construction throughout the years has been very limited. The graph below compares the improvement of labor productivity between the years 1964 and 2012 between construction and other industries:
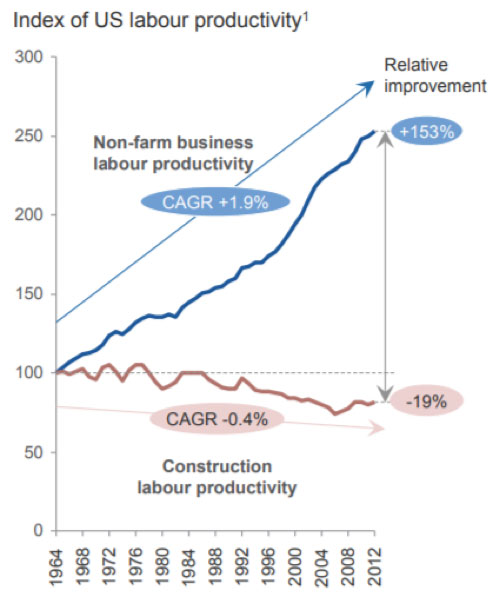
The lack of competitiveness within the construction industry can be explained by reviewing some of their challenges:
Lack of innovation and delayed adoption: you may not be aware of it, but the profitability margin for the construction industry is quite low. This fact generates an exclusive focus on present projects and lack of interest in long-term opportunities or investments. Additionally, small and medium construction companies will not adopt any new technologies or processes until bigger organizations with larger budgets have proven success with new implementations, hence, the industry overall delays adoption.
Informal processes or insufficient rigor and consistency in process execution: as every project is unique, construction companies tend to ignore the benefits of standardizing processes.
Insufficient knowledge management: past experiences and learning points from previous projects get lost and projects continue to rely heavily on the individual experience and capabilities of the Project Manager.
Weak project monitoring: in a car manufacturing environment, for example, issues in the production line and their root causes are immediately identified and corrected, operations are continuously tracked, and large amounts of data are collected and put to use. In construction, this is not the case. In some cases, it takes days, weeks and even months before issues and potential delays are identified and then additional time until a solution can be found. Additionally, companies deploy one or more employees onsite to report on the progress of a project, but in many cases this information is subjective, as well as costly and time consuming to acquire.
Limited collaboration with suppliers: construction companies generally try to establish long-term relationships with their suppliers; however, purchasing decisions and behaviors are usually taken on a project by project basis, resulting in inefficiencies in the supply chain.
Over the last few years, new technologies such as 3D printing, robotics and artificial intelligence have begun to make their way into the construction industry to tackle these challenges and help the industry evolve. This is also the case for drones and the use of aerial data in construction projects. These technologies combined with machine learning and advanced data analytics are already having a significant impact on the digitalization of projects.
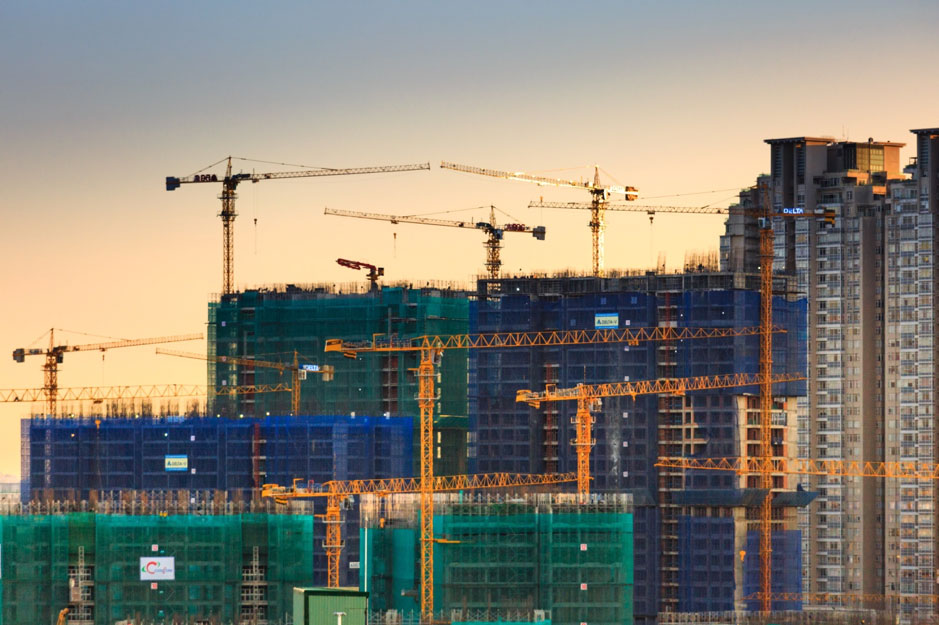
”In the long-term, AI and analytics have boundless potential use cases in Engineering & Construction. Machine learning is gaining some momentum as an overarching use case (that is, one applicable to the entire construction life cycle, from pre-construction through O&M), particularly in reality capture as well as for comparison of onsite field conditions with plans. Indeed, by applying machine learning to an ongoing project, schedules could be optimized to sequence tasks and hit target deadlines, and divergences from blueprints could be caught closer to real time and corrected.
In the immediate future, we expect AI’s proliferation in the Engineering & Construction sector to be modest. Few leaders have the processes, resources, and existing data strategies in place to power the necessary algorithms and meaningfully implement this technology. However, the potential impact is so large that the industry can no longer afford to ignore it. AI methods are increasingly able to work across industries, elevating the threat of competition from non-traditional market entrants. And a narrow set of start-ups are already gaining market traction using AI-focused approaches.” (Blanco, Mullin, Pandya, Parsons, & Ribeirinho, 2018)
For drones and aerial data analytics, there are several applications already deployed at scale by industry leaders, such as ground surveying, construction progress monitoring, asset inspection and general mapping.
As with the adoption of most technologies, there are implementation challenges that arise, such as:
Local regulations: currently, every country has different regulations regarding the use of drones for commercial activities, which makes it a challenge to implement at global scale efficiently.
Data Protection: in the case of Europe, the GDPR regulation constrains certain applications for the use of aerial data.
Liability: when operating close to traffic routes or urban areas, operating errors could cause serious consequences and therefore, creating the need for compulsory insurance policies for drone operators.
Technical Know-how: a very important aspect as well, as the user will need to make many choices regarding the hardware (drone and sensors), the workflows (automated or manual operation), photographical requirements (resolution among others), photogrammetric requirements (e.g. control points, RTK, georeferenced images) and further processing of data (e.g. point clouds, orthomosaics).
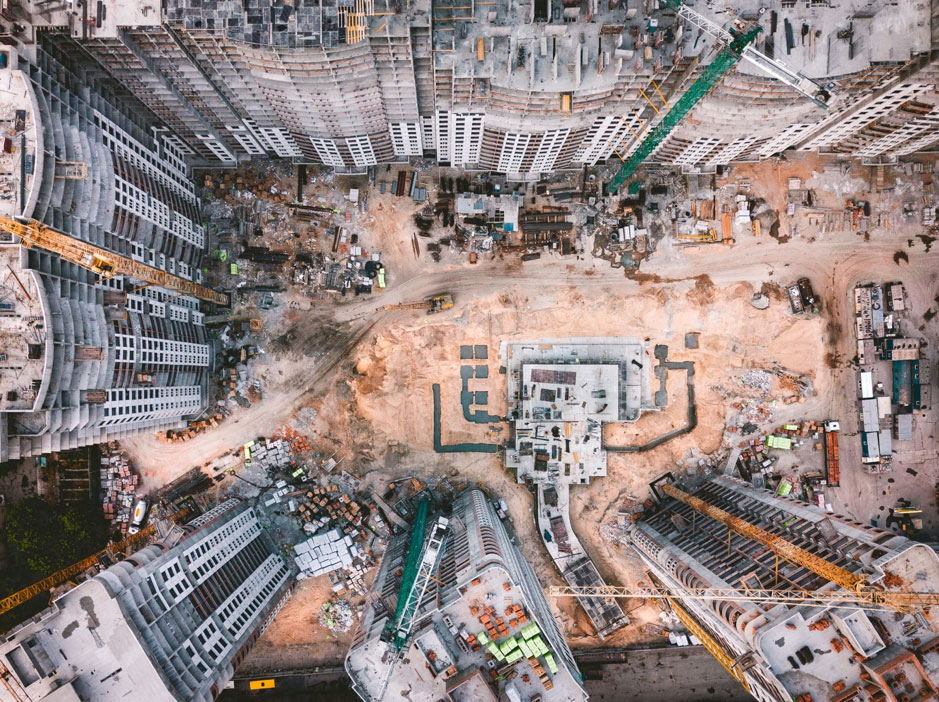
By tackling these implementation challenges, for example, by implementing a new cross-EU drone regulation, would greatly help. The future of aerial data in construction looks bright if a new adopted regulation could increase safety, but at the same time allow for usage expansion while improving the standards definition for the industry. The vision of an automated, connected and digital construction site is becoming more real and at some point, aerial data and all the other technologies will no longer be a “nice to have” but a “must have” for every infrastructure project.
How project delays affect your bottom line
Project delays are a common denominator in the industry and there are multiple reasons why a project can run late:
Change in project scope: Change in project scope could be due to poor initial project scope definition, miscalculation of inherent uncertainties, project funding issues, change in the interest of the client or a force majeure. This could result in a change order that may successively lead to changes in project deliverables, budget and even the entire project team.
Thus, any modification or change within the project scope throughout execution will cause the whole initial project set-up to be revised, which leads to more time, resources and cost against the initial baseline to complete the work.
Project complexity: Complexity can be outlined in terms of scale of the project. Most mega construction projects i.e. dams, skyscrapers, nuclear power stations etc. tend to possess longer implementation. This can then be significantly affected by changes in material prices, exchange rates and inflation rates.
As a result, there may be increases in cost and long chains of negotiation which eventually cause a delay in overall duration of the construction project.
Inadequate planning: This can be explained as identifying and organizing the necessary resources (human, time, equipment, sub-contractors, etc.) to deliver the desired outcome.
There are many professionals involved in the construction process, so a planner has to insure that every aspect of these is already incorporated in the planning process to obtain the maximum outcomes.
Inappropriate project schedule: Scheduling shows not only the logical order in which the activities are to be carried out, but also enables the stakeholders to monitor progress.
Inaccurate Engineering estimates: The detailed investigative study, design expertise, scope of work, quantity calculations and proper planning are required to obtain the Engineering estimates.
Inaccuracies in estimation will cause a cost overrun and subsequently result in delay in the duration of the project.
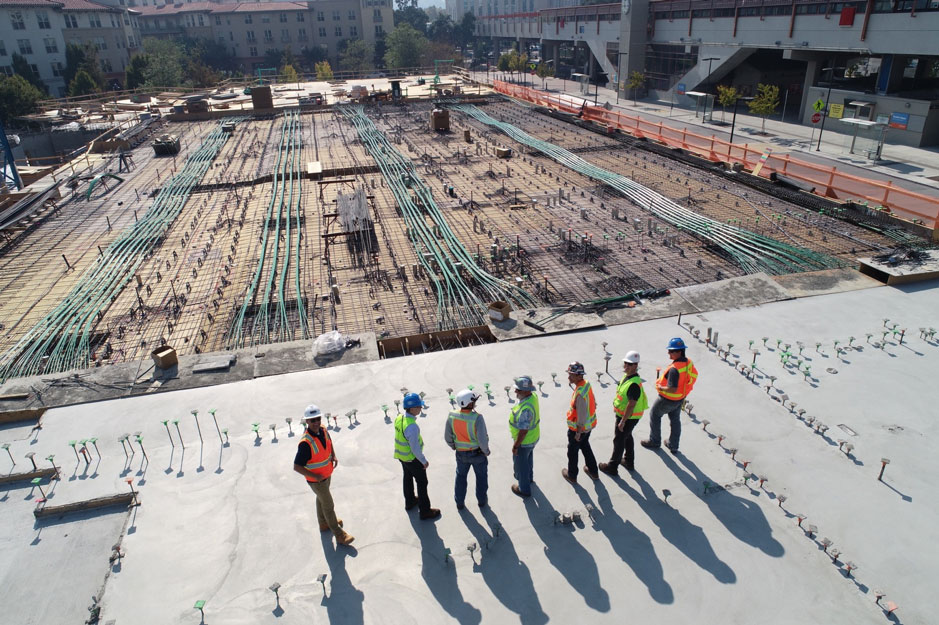
Indeed, by implementing aerial data analytics and collaborative platforms during all phases of a construction project, delays and costs overruns can be minimized. A complete digitization of the project from design phase to operations and maintenance will increase collaboration across stakeholders, provide objective and data-driven information to facilitate decision making and information management. By implementing strict project monitoring, the overall financial and timely success probability of the project is increased.
VIA IMC Case Study
VIA IMC is the infrastructure innovation platform of Vinci. VIA IMC has decades of hands-on experience in planning, building and operating complex infrastructures. They are of the opinion that road construction must become more digital to save resources and make working on construction sites safer.
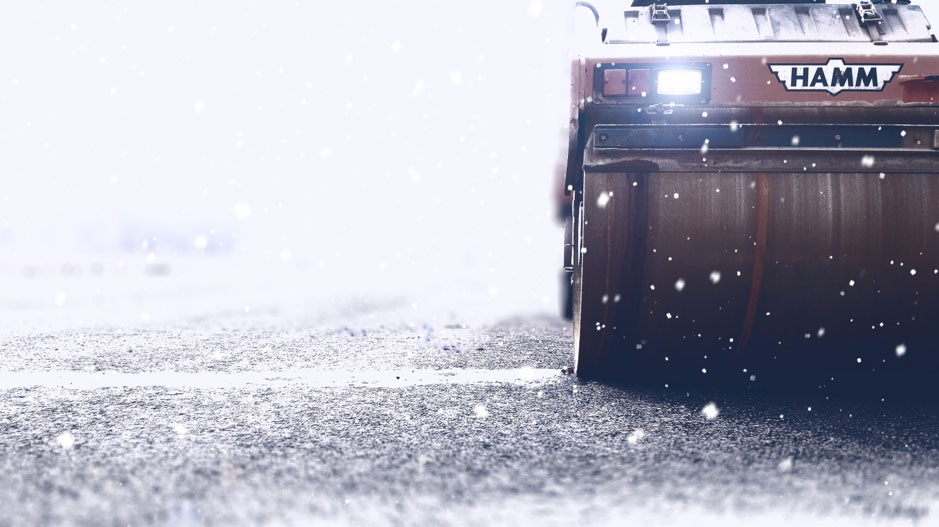
In 2018, Sitemark and VIA IMC officially started a long-term partnership and with it, AVUS.DIGITAL was born. From the initial concept, to construction and operation, AVUS is the digital tool for advanced infrastructure construction, combining modern technologies such as drones, smartphones and 3D models into a single platform.
The combination of VIA IMC’s in-depth industry knowledge and Sitemark’s technical expertise were the perfect combination to deploy aerial data technology at scale for Eurovia, Germany and hopefully in the future, for more entities of the Vinci Group.
Why are Eurovia entities moving to aerial data?
Traditional surveying technologies can reach higher accuracy and thus, are often more easily accepted by regulatory entities and contracting authorities. Contractual regulations oftentimes require certain instruments to be used. While the low tolerance of accuracy errors might be significant for certain assignments, e.g. determining the layer height of concrete road surfaces or staking-out of boundaries, for many daily tasks in the construction industry, a lower accuracy is sufficient. High precision GPS receivers can also reach similar accuracies from the 3D point clouds they generate.
Modern unmanned aerial vehicles (UAVs) can cover vast areas in little time while acquiring images, increasing the data acquired per minute ratio. Each flight results in millions of points after processing. In common construction software, relevant information can be extracted out of a point cloud and the acquisition of objects within the area of interest does not need to be preplanned, as the projection of entire areas is being covered.
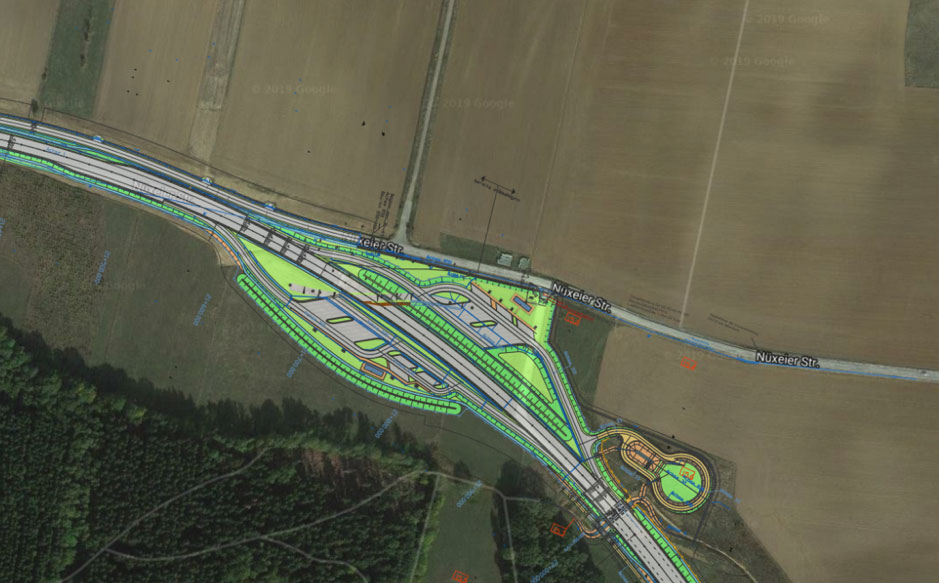
Figure 2. CAD overlay of construction site
This results in an often easily overlooked point and in our opinion, the most valuable contribution of aerial data to BIM: acquiring and processing aerial data supplies the same accurate information to all the stakeholders within the construction project. The combination of deliverables, such as a high-resolution orthomosaic and a dense 3D point cloud, can be used and interpreted for many different functions. Volumes and masses can be used for the billing process and QTO (quantity take-off). 3D point clouds can be used by engineering firms to create drawings, re-plan entire areas and create BIM models. Construction managers can see the state of the site, overlay orthomosaics with the final drawings to determine weakness in the processes and perform comparisons. Senior construction managers, CEOs and Board members can oversee numerous projects with ease, saving time, money and having the opportunity to steer projects at critical points.