1. Hot spots are most common
Hot Spots – A single overheated cell on a panel often caused by soiling or bird droppings
Hot Spots indicate a defect at cell level, where one or several cells have a higher temperature than the neighbouring ones. Depending on the temperature difference (temperature delta) between the heated and normal cell, a Hot Spot may indicate a defect of varying levels of severity. At Sitemark, our software differentiates between Hot Spots (where only one cell appears to be impacted) and Multi Hot Spots (several cells of one panel are unambiguously impacted, obviously more concerning).

Causes
The causes of a Hot Spot are numerous. Some causes can be reversible, while others not. Thermal images usually aren’t sufficient to identify the causes of Hot Spots, but thanks to the use of visual (RGB) photos, we are capable of identifying the main cause for Hot Spots.
The most common causes come from external elements that cast a shadow on the panel. As a cell gets covered by shade, it turns into a resistor and will dissipate the energy produced by the other cells in the string. At Sitemark, the causes are identified according to the following categories:
· Soiling of the panels: deposits of dirt, leaves, etc.
· Droppings: Bird droppings, which is frequent at the seaside or in industrial areas that involve food processing plants

· Vegetation: overgrown grass or plants that grow in front of panels, or between the panels
· Shadowing: external elements casting a shadow on the panels. Classic examples include physical elements bordering the sites, such as electrical poles, antennas, high tension cables, fences, trees, etc.
· Physical defects: Degraded panels or cells will show Hot Spots, but the underlying reason may not be visible to the naked eye, let alone from drone pictures. These would include snail trails, micro-cracks, delamination, back-sheet issues, shattered glass, etc.
Remedial Actions
Depending on the cause, suggested remedial actions vary:
· Should the Hot Spots be caused by soiling and droppings, cleaning the panels can be sufficient to bring the panel back to their nominal efficiency.
· Vegetation: cutting the grass should also be sufficient. However, some defects that are deemed reversible can bring long term damage to the panels if not treated fast enough. We estimate that one season will be enough to turn a reversible Hot Spot into a non-reversible one, hence the importance of cleaning and cutting the grass at least once a year.
· Shadowing: as causes of shadowing are usually external elements, no remedial action can be taken in most cases. The impacted panels should be monitored to assess whether the losses don’t dissipate too much of the production of non-impacted panels. The impacted panels may have to be replaced more regularly if the layout of the plant cannot be adapted to avoid the shadowed areas.
· Physical defects: Depending on the severity of the Hot Spot, the age of the plant and the underlying cause, physical defects may justify a warranty claim towards the manufacturer. Acceptance criteria for warranty claims differs from one manufacturer to the next, but a common threshold is a temperature delta of at least 20 degrees Celsius between overheated cells and normally functioning ones.
Losses
Overheated cells acting as a resistor will dissipate energy generated by the other cells. Such cells will have an impact on the production of the full string that the panel is part of.
We generally assume that the losses will be proportional to the delta temperature of the Hot Spot, relative to the level of production of the plant. One order of magnitude to keep in mind is the assumption that one Hot Spot alone on a string may cause a loss of production of up to 90% of the nominal production of one panel.
2. String issues have the most impact
String issues represent a group of panels disconnected from the inverter, often caused by a blown fuse or bad connection.

Symptoms
One group of panels is warmer than comparable panels by a few degrees. Temperature is uniform across the impacted group of panels.
Causes
The full string is disconnected and thus, gets warmer because the solar irradiance isn’t converted into electricity. This may occur because of several issues, such as:
· A blown fuse
· A disconnected cable
· A damaged or burnt welding point
· A physical issue in a connection box or at the inverter
· Any issue that could cause a physical disconnection or prevent current from flowing through the string
Remedial Actions
Start with a thorough check of the connections of the string. Since these issues cause extreme losses and are often easy to fix, they should be treated with the highest level of priority.
Losses
As a string of panels is disconnected, the losses amount to the production of all of these panels, for as long as the string issue has existed.
3. Potential Induced Degradation (PID) and Suspected PID are the most interesting
Potential Induced Degradation and Suspected PID are an early-stage defect caused by a voltage difference between the cells and the frame of the panels.
Symptoms
Definition and threshold for the classification of PID vary throughout the industry. At Sitemark, we not only mark PID but also panels that show an early-stage behaviour similar to PID. These show warmer cells close to the edges of the panels, indicating that the cause of the temperature increase can be found in a voltage difference.
Our threshold is that we mark panels that have more than one edge impacted by such an effect.

Panels show a checkerboard pattern on the thermal images. Significant temperature differences are visible between the cells. This type of defect usually impacts several contiguous panels, and in all likelihood at the end of a string, ie. close to the negative pole of the string.
Causes
Potential Induced Defects (PID) are caused by a voltage difference between the cells and the frame of the panels. This difference may cause residual leakage current to flow through the cells and impact the yield significantly.
This effect is thought to be mostly impacted by the following parameters:
· Grounding of the panel frames, the poles, etc.
· The choice of the inverter and its working mode, more particularly the potential differences between the poles and the ground that the inverter is set at.
· Panel design, including the type of insulation used, the silicon wafer type, mechanical design of the frame, etc.
Remedial Actions
Not all the likely causes of PID issues can be acted upon, which leaves the operator with limited choice.
The main remedial actions can include:
1. Check the grounding of the frames, panel rows and inverters to assess whether the grounding can be improved. A thorough inspection of the impacted strings and rows may lead to some insight about the underlying causes of PID.
2. As a short term fix, swap panels from the positive end to the negative end of the string to avoid physical problems building up in the panels over time.
3. Consider changing the working mode of the inverters if possible, to change the voltage difference between ground and inverter poles.
4. Consider commercial solutions that inject a very small reverse current at night to counteract the effects of PID.
5. For Suspected PID, no short-term actions are recommended. These defects can also simply indicate the normal wearing of the panels due to the age of the installation. However, proper monitoring of the status of these panels is recommended, to see how the situation evolves.
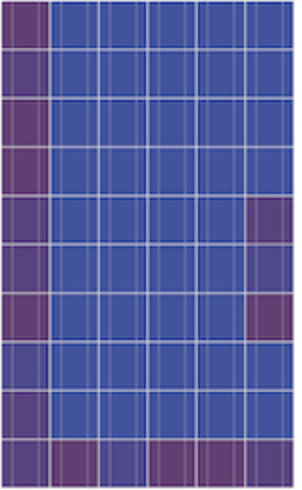
Losses
Leak currents and overheating of cells will dissipate energy that the inverter would otherwise convert. A commonly accepted estimate in the scientific community is that losses per panel impacted may be as high as 30%. PID issues tend to worsen over time.
For Suspected PID, the temperature differences undoubtedly indicate losses, but it is assumed that such panels will cause lower losses than actual mature PID.
Get in touch to discover how we can help optimize your solar site.
